DESCRIPTION
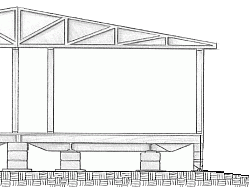
The pier and ground anchor foundation system has long been the common and accepted manufactured home support and anchorage system. It adapts easily to local site conditions, does not require a great deal of dimensional precision, and goes into place quickly. In the most frequently used configuration, piers are designed by our engineers to be installed under the main beams of the home sections, under the mating line of multi-section homes and at other points designated by the home manufacturer. Perimeter piers or blocks may also be a part of the home’s support system.
The most common pier types are steel jack stands or hollow core concrete masonry blocks with open cells placed vertically and stacked one on top of the other to the required height. These can be single stacks of blocks or double stacks, laid up in an interlocking configuration. Concrete block piers over 36 in. high should be configured as double block piers. Piers over 80 in. high take special considerations by the engineer.
Another pier type is the pyramid-shaped open frame, steel type with a support plate on top of an adjustable rod at the apex. The steel pyramids come in several heights and support prescribed/rated load capacities based on manufacturer’s testing. The pier height and building weight dictate the allowable spacing between the piers.
Ready to Order? If you are ready to order foundation plans, you may place your order by clicking here.
Piers set on square footers or pads on the ground spread the load from a pier over a larger area, making a more stable base. The square pad footers may be concrete, either poured in place or precast, preservative-treated wood, acrylonitrile butadiene styrene (ABS), or other materials approved by the local building authority and designed by our engineers. The spacing of the piers and the allowable bearing capacity of the soil determine the size of the footer or pad. The piers are typically vary depending on home design, local soil characteristics, and roof snow load.
The spacing of the anchors and the strap is specified by our engineers based on the size of the home and the wind zone. In HUD wind zones II and III, vertical straps from the sidewall of the home to ground anchors may be required in conjunction with the straps from the I-beam to the ground anchor. Our engineering analysis will show the tie-down sizes, capacities, and spacings on the plans we create for you.
COST OF CONSTRUCTION
The pier and anchor support system is the least initial cost for providing a support system for manufactured homes.
REAL PROPERTY CLASSIFICATION
In some instances, lenders and state and federal agencies do not consider pier and ground anchor support systems a real property foundation. Some exceptions are acceptable like cases where the anchors are held in place by means other than the soil alone, such as encasing the anchors in a concrete slab. These types of approaches are explored by our engineers when we design your plans.
INSTALLATION
The installation of a pier and ground anchor foundation system is frequently accomplished in one working day.
WIND LOAD RESISTANCE
On non-proprietary systems, the pier and anchor system is the one most often specified by our engineers as an effective means to resist wind forces.
GRAVITY LOAD RESISTANCE
A pier and anchor foundation supports gravity loads (live and dead) adequately. Our engineers take into account the bearing strength of the soil, and that the piers are properly spaced, and there are appropriate perimeter piers installed as required by the home manufacturer and the authority having jurisdiction.
SEISMIC LOAD RESISTANCE
Since the HUD standards have no provisions for seismic resistance design, almost all manufactured housing, (and, therefore, most pier and anchor installations) is not designed specifically to withstand seismic loads. Our engineers, however, analyze that a manufactured home is capable of resisting the highest seismic forces in the model building codes for your specific geographic region.
FLOOD RESISTANCE
The foundation type is suitable for use in flood plain areas when FEMA-recommended designs or designs meeting FEMA’s performance criteria are used. FEMA suggests taking the following precautions when a home is located in a flood plain: the anchor system should be designed to resist uplift floatation, collapse, and lateral movement under saturated soil conditions; and the floor level should be set above the 100-year base flood elevation. Under no circumstances should the home be located in a floodway.
FROST PROTECTION
In areas where frost is a design issue, individual anchors and footers under the piers are designed to below the frost line and bear on earth below that depth. As an alternative to running the footers below the frost line, holes for the footers may be dug to the frost depth and then back filled to the surface with gravel or other material that will not retain moisture. Another option is to insulate the area around the crawl space. This would eliminate the need to run the anchors and footings below the frost depth.